لوله فولادی گالوانیزه یکی از حیاتیترین اجزای زیرساختی در صنایع نفت، گاز، پتروشیمی، تأسیسات ساختمانی و شبکههای آبرسانی است. این لوله با پوششی از فلز روی (Zinc) پوشانده میشود تا در برابر رطوبت، خوردگی و مواد شیمیایی مقاوم باشد؛ ویژگیای که در محیطهای صنعتی خورنده، ارزش آن را چند برابر میکند.
آنچه لوله گالوانیزه را نسبت به سایر انواع لوله فولادی متمایز میکند، ترکیب منحصربهفرد دوام مکانیکی با محافظت شیمیایی است. در پروژههایی که دسترسی به لولهها دشوار است یا امکان تعمیر و تعویض محدود است، انتخاب این نوع لوله، تصمیمی هوشمندانه و بلندمدت محسوب میشود. از خطوط انتقال سیالات گرفته تا سازههای فلزی در معرض هوای آزاد، لوله فولادی گالوانیزه نقشی حیاتی و غیرقابل جایگزین ایفا میکند. اگر میخواهید با فرآیند تولید، استانداردها، کاربردها و جدیدترین راهکارهای افزایش عمر مفید این لوله آشنا شوید، ادامه مطلب را از دست ندهید.
لوله فولادی گالوانیزه چیست؟ تفاوتها با لوله معمولی در صنایع سنگین
لوله فولادی گالوانیزه نوعی لوله است که در فرایند آن، ابتدا تولید لوله فولادی معمولی انجام میشود و سپس لایهای از فلز روی به سطح بیرونی آن افزوده میشود تا در برابر خوردگی و عوامل محیطی مقاوم شود. برخلاف لولههای فولادی سیاه یا ساده، این لولهها برای استفاده در محیطهای مرطوب، خطوط انتقال آب، گاز و هوای فشرده کاربرد دارند. تفاوت اصلی این دو نوع لوله در میزان مقاومت آنها در برابر زنگزدگی و عمر مفیدشان است.
در صنایع سنگین که تماس با رطوبت، مواد شیمیایی و بخارات صنعتی اجتنابناپذیر است، استفاده از لولههای گالوانیزه به دلیل پوشش محافظتیشان، ضریب ایمنی بیشتری ایجاد میکند. این پوشش بهصورت گالوانیزه گرم یا گالوانیزه سرد انجام میشود که نوع گرم آن دوام بالاتری دارد. از منظر اقتصادی نیز، هرچند هزینه اولیه گالوانیزه کردن بیشتر است، اما در درازمدت با کاهش هزینههای تعمیر و جایگزینی، بهصرفهتر خواهد بود. بنابراین در پروژههای عمرانی و صنعتی سنگین، انتخاب لوله فولادی گالوانیزه نسبت به لوله فولادی معمولی تصمیمی هوشمندانه و فنی است.
چرا صنایع سنگین از لوله گالوانیزه استفاده میکنند؟ کاربردها در نفت، گاز و پتروشیمی
لوله فولادی گالوانیزه به دلیل مقاومت بالا در برابر شرایط سخت محیطی، بهویژه در صنایع نفت، گاز و پتروشیمی، یکی از انتخابهای اصلی در طراحی خطوط انتقال محسوب میشود. این لولهها بهخوبی در برابر خوردگی، رطوبت و بخارات خورنده مقاومت میکنند. در بسیاری از صنایع سنگین، نیاز به لولههایی با طول زیاد و ساختار مستحکم باعث شده از روشهای خاصی مانند تولید لوله اسپیرال برای ساخت لولههای فولادی استفاده شود که در ادامه با گالوانیزه کردن، مقاومت آنها چند برابر میشود.
لوله اسپیرال به دلیل شکل مارپیچی درز جوش، توان تحمل فشار بالا را دارد و زمانی که این نوع لوله گالوانیزه شود، هم ایمنی و هم دوام را برای پروژه به ارمغان میآورد. از آنجا که در صنایع پتروشیمی دسترسی به لولهها محدود است، استفاده از لولههای گالوانیزه باعث کاهش زمان توقف عملیات و افزایش عمر تجهیزات میشود. این ویژگیها، آن را به گزینهای بیرقیب برای محیطهای صنعتی خورنده تبدیل کردهاند.
از فولاد تا لوله گالوانیزه؛ فرایند گالوانیزه گرم به زبان ساده
فرآیند گالوانیزه کردن گرم یکی از روشهای اثباتشده برای افزایش مقاومت لوله فولادی در برابر خوردگی و رطوبت است. در این فرآیند، پس از تولید اولیه لوله، سطح آن با روشهایی مانند اسیدشویی کاملاً پاکسازی میشود و سپس در حمامی از روی مذاب (با دمای حدود ۴۵۰ درجه سانتیگراد) غوطهور میگردد. این عملیات باعث ایجاد پوششی یکنواخت از فلز روی بر سطح لوله میشود. برخلاف روشهای رنگآمیزی یا پوششهای اپوکسی که فقط یک لایه سطحی ایجاد میکنند، گالوانیزه گرم باعث ایجاد پیوند متالورژیکی بین فلز روی و فولاد میشود. این ویژگی باعث میشود لوله در برابر ضربه، سایش و عوامل محیطی مقاومت بالاتری داشته باشد.
بسیاری از مهندسان و تولید کننده لوله های چدنی نیز به دلیل شباهت کاربردی، به سوی تولید و پوشش گالوانیزه برای برخی قطعات هدایت شدهاند. فرآیند گالوانیزه گرم نه تنها از نظر صنعتی مقرونبهصرفه است، بلکه استانداردهایی مانند ASTM A123 نیز آن را تأیید کردهاند و به عنوان روشی مرجع برای محافظت در برابر زنگزدگی محسوب میشود.
مقایسه گالوانیزه گرم و گالوانیزه سرد؛ کدام روش برای صنعت بهتر است؟
در صنعت گالوانیزهکاری، دو روش اصلی برای اعمال پوشش فلز روی وجود دارد: گالوانیزه گرم و گالوانیزه سرد. در روش گرم، لوله فولادی در حمام مذاب روی غوطهور میشود که نتیجه آن پوششی یکنواخت، ضخیم و با دوام بسیار بالا است. در مقابل، در روش سرد، روی با استفاده از الکترولیز به سطح لوله میچسبد و بیشتر برای محیطهای کمخطر مناسب است. در پروژههایی که در معرض شرایط محیطی شدید مانند باران اسیدی یا تماس مستقیم با مواد شیمیایی قرار دارند، استفاده از گالوانیزه گرم توصیه میشود.
لوله فولادی گالوانیزه گرم، با ضخامت بیشتر پوشش، مقاومت بیشتری در برابر خوردگی دارد. همین ویژگی باعث شده است که در صنایعی مانند تولید لوله کاروگیت، که لولهها در زیر زمین یا محیطهای مرطوب کار گذاشته میشوند، گالوانیزه گرم اولویت داشته باشد. علاوه بر این، گالوانیزه گرم از نظر استانداردهای بینالمللی مانند ISO 1461 نیز ارجحیت دارد و پایداری بیشتری در طول زمان ارائه میدهد.
استانداردهای جهانی تولید لوله فولادی گالوانیزه؛ چه معیارهایی حیاتیاند؟
تولید لوله فولادی گالوانیزه باید مطابق با استانداردهای جهانی انجام شود تا عملکرد، ایمنی و دوام آن در پروژههای صنعتی تضمین شود. استانداردهایی نظیر ASTM A53، BS EN 10255 و DIN 2440، معیارهای دقیقی برای ترکیب شیمیایی فولاد، ضخامت لایه گالوانیزه، روش تست کیفیت و نحوه اجرای فرآیند پوشش ارائه میدهند. هر کارخانهای که خط تولید لوله گالوانیزه راهاندازی میکند، باید تجهیزات پیشرفته برای کنترل دما، زمان غوطهوری در روی، تست اسپری نمک و بررسی یکنواختی پوشش در اختیار داشته باشد.
این استانداردها همچنین بر نوع تستهای کششی، تست خمیدگی و ضربه نیز تأکید دارند تا مطمئن شوند که لولهها برای شرایط سخت صنعتی مناسب هستند. رعایت دقیق این معیارها باعث میشود محصول نهایی برای صادرات نیز قابل قبول باشد. توجه به جزئیات فنی در خطوط تولید، از انتخاب مواد اولیه گرفته تا کنترل نهایی، پایهی تولید لولههای استاندارد و بادوام است که در تمامی صنایع زیرساختی نقش کلیدی دارند.
راهکارهای افزایش طول عمر لوله گالوانیزه در محیطهای صنعتی خورنده
افزایش طول عمر لوله فولادی گالوانیزه در محیطهایی با رطوبت بالا، بخارات شیمیایی یا دمای متغیر، مستلزم اجرای راهکارهای حفاظتی هوشمندانه است. یکی از مؤثرترین روشها، استفاده از پوششهای اپوکسی یا پلیاتیلن پس از گالوانیزه کردن است که مانند لایهای دوم، سطح فلز را در برابر مواد خورنده عایق میکند. در صنایعی که خاک یا آب خاصیت اسیدی یا قلیایی دارند، استفاده از روش حفاظت کاتدی، مانند نصب آند فداشونده، میتواند فرآیند خوردگی را بهطور قابلتوجهی کاهش دهد.
انتخاب مناسب محل اجرا و نصب لوله، شامل فاصله از منابع شیمیایی و تهویه کافی، نقش مهمی در جلوگیری از زنگزدگی موضعی دارد. استفاده از آبشورزدایی در خطوط انتقال آب و بهرهگیری از نوارهای ضدخوردگی در نقاط اتصال نیز از جمله اقدامات مکملی هستند که توسط متخصصان توصیه میشوند. این اقدامات در کنار بازرسی منظم و تعمیرات پیشگیرانه، عمر مفید لولهها را تا دو برابر افزایش میدهند و هزینههای بلندمدت نگهداری را به حداقل میرسانند.
عیوب رایج در فرآیند گالوانیزهکاری؛ راههای تشخیص و رفع آنها
در فرآیند گالوانیزه گرم، با وجود مزایای فراوان، در صورت نبود کنترل دقیق، برخی عیوب فنی ممکن است بروز کنند که بر کیفیت نهایی لوله فولادی گالوانیزه تأثیر میگذارند. یکی از شایعترین این مشکلات، پوشش ناهموار یا ایجاد برجستگیهای سطحی است که معمولاً ناشی از عدم تمیزکاری صحیح یا دمای غیراستاندارد روی مذاب است. عیب دیگر، پوستهپوسته شدن یا جدا شدن لایه روی در اثر شوک حرارتی یا خنککاری سریع میباشد. همچنین در برخی موارد، ترکهای مویی در سطح لوله دیده میشود که اغلب به دلیل تنشهای داخلی یا جوشکاری غیراصولی ایجاد میشوند.
برای تشخیص این نواقص، تست چشمی دقیق، استفاده از رنگهای نافذ (dye penetrant) و آزمونهای ضخامتسنجی با ابزارهای دیجیتال ضروری است. در کارخانههای حرفهای، واحد کنترل کیفیت باید هر دسته از لولهها را طبق استانداردهای ISO و ASTM آزمایش کند. رفع این عیوب، نهتنها باعث افزایش ایمنی کاربردی میشود، بلکه از برگشت خوردن محصول در صادرات نیز جلوگیری میکند.
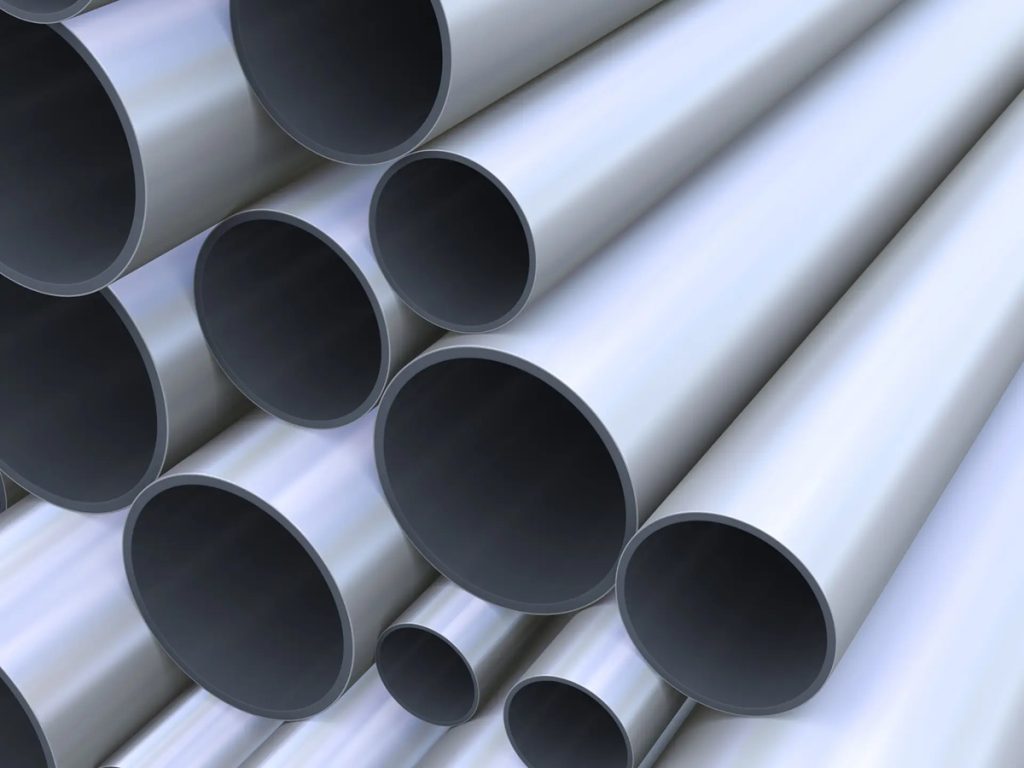
تاثیر کیفیت روی (Zinc) بر خواص نهایی لوله گالوانیزه
کیفیت فلز روی مورد استفاده در فرایند گالوانیزهکاری، تأثیر مستقیمی بر خواص نهایی لوله فولادی گالوانیزه دارد. هرچه خلوص روی بالاتر باشد (مثلاً بیش از ۹۸.۵ درصد)، مقاومت لایه پوششی در برابر رطوبت و مواد شیمیایی بیشتر میشود. همچنین خلوص بالای روی موجب یکنواختی لایه و چسبندگی بهتر آن به فولاد پایه میگردد. طبق استانداردهای بینالمللی نظیر ASTM B6، استفاده از روی کمکیفیت یا آمیخته با ناخالصیهایی مانند آهن، آلومینیوم یا قلع، باعث کاهش ضخامت پوشش و کاهش عمر مفید لوله خواهد شد. همچنین این موضوع میتواند منجر به خوردگی زودهنگام، پوستهپوسته شدن یا حتی ایجاد حفره در سطح لوله شود. در کارخانههای معتبر، روی مصرفی بهصورت گواهیشده و با آنالیز آزمایشگاهی وارد چرخه تولید میشود. انتخاب روی با کیفیت برای صنایع زیرساختی، بهویژه در مناطق شرجی یا محیطهای شیمیایی، نهتنها توصیه میشود، بلکه الزام فنی محسوب میگردد. بنابراین کیفیت روی، عنصری کلیدی در تضمین عملکرد و پایداری لوله در کاربردهای صنعتی است.
بهترین روشهای تست کیفیت لوله گالوانیزه؛ از تست اسپری نمک تا آزمون ضربه
ارزیابی کیفیت لوله فولادی گالوانیزه از طریق آزمونهای فنی استاندارد انجام میشود که هدف آنها تضمین دوام، ایمنی و انطباق با شرایط کاری واقعی است. یکی از روشهای پرکاربرد، تست اسپری نمک (Salt Spray Test) است که بر اساس استاندارد ISO 9227 انجام شده و میزان مقاومت پوشش روی را در برابر خوردگی شبیهسازی میکند. در این آزمون، نمونه لوله در محفظهای با مهنمک قرار گرفته و میزان زنگزدگی پس از گذشت زمان مشخص، بررسی میشود.
آزمون ضخامتسنجی نیز با استفاده از دستگاههای دیجیتال انجام میشود تا یکنواختی لایه روی و میزان مطابقت با استانداردهای DIN و ASTM ارزیابی گردد. علاوه بر این، آزمون ضربه یا Bending Test برای بررسی چسبندگی پوشش روی در برابر تنشهای مکانیکی ضروری است. ترکیب این تستها در کنار کنترل چشمی و بررسی جوشها، دید دقیقی از کیفیت محصول به مهندسان کنترل کیفیت میدهد. بهکارگیری این روشها، پایهگذار تولید مطمئن و استاندارد در پروژههای صنعتی است.
جمعبندی: لولهای برای همهی فصول؛ انتخابی هوشمندانه در هر پروژه صنعتی
لوله فولادی گالوانیزه، با اتکا به ساختار مستحکم فولاد و پوشش محافظ فلز روی، یکی از قابلاعتمادترین گزینهها در طراحی و اجرای شبکههای صنعتی به شمار میرود. این لولهها بهویژه در شرایطی که رطوبت، مواد شیمیایی یا سایش مکانیکی وجود دارد، عملکردی بینقص از خود نشان میدهند. فرآیند گالوانیزاسیون، نهتنها عمر مفید لوله را به طرز چشمگیری افزایش میدهد، بلکه هزینههای تعمیر و نگهداری را نیز کاهش میدهد؛ عاملی کلیدی در پروژههایی با بودجه محدود یا دسترسی دشوار.
با رعایت استانداردهای تولید، استفاده از روی با خلوص بالا، تستهای دقیق کیفیت و انتخاب ضخامت مناسب، میتوان اطمینان یافت که لوله فولادی گالوانیزه در هر پروژهای، از تأسیسات ساختمانی تا صنایع سنگین، نقش خود را بهخوبی ایفا خواهد کرد. در دوران کنونی که بهرهوری، پایداری و هزینه مؤثر اهمیت بالایی دارند، استفاده از این نوع لوله، پاسخی عملی و اثربخش به نیازهای زیرساختی مدرن است. حال زمان آن فرا رسیده تا با آگاهی کامل، بهترین انتخاب را برای زیرساختهای حیاتی خود داشته باشید.
سوالات متداول
۱. لوله فولادی گالوانیزه چه تفاوتی با لوله فولادی معمولی دارد؟
لوله گالوانیزه دارای پوشش فلز روی است که آن را در برابر خوردگی مقاوم میکند، در حالیکه لوله معمولی فاقد این محافظ است.
۲. آیا لوله گالوانیزه برای انتقال گاز مناسب است؟
بله، بهویژه در فشارهای پایین و محیطهای مرطوب؛ اما باید مطابق استاندارد نصب شود.
۳. پوشش گالوانیزه چقدر عمر میکند؟
بسته به محیط، ضخامت پوشش و کیفیت تولید، بین ۲۰ تا ۵۰ سال دوام دارد.
۴. گالوانیزه گرم بهتر است یا سرد؟
در محیطهای صنعتی، گالوانیزه گرم بهدلیل مقاومت بالاتر، انتخاب بهتری است.
۵. آیا لوله گالوانیزه قابل بازیافت است؟
بله، هم فولاد و هم فلز روی قابل بازیافتاند و در صنایع سبز اهمیت دارند.