تولید گرانول پلاستیک نقطه آغاز تحولی عظیم در زنجیره تأمین صنایع پلیمری است. در جهانی که بازیافت و بهرهوری منابع اهمیت فزایندهای دارد، این فرآیند نقشی کلیدی در تبدیل مواد خام یا ضایعات پلاستیکی به محصولاتی با قابلیت پردازش مجدد ایفا میکند. گرانولها، که به شکل دانههای کوچک و یکنواخت تولید میشوند، پایه اصلی ساخت قطعات تزریقی، فیلمهای بستهبندی، لولههای صنعتی و تجهیزات خانگی بهشمار میروند.
فرآیند تولید گرانول نهتنها وابسته به انتخاب دقیق مواد اولیه است، بلکه مستلزم کنترل دقیق دما، فشار، رطوبت و پارامترهای فیزیکی در طول عملیات اکستروژن و خنککاری است. شناخت این فرآیند برای فعالان حوزه بازیافت، صنایع خودروسازی، کشاورزی، پزشکی و بستهبندی، یک ضرورت حرفهای بهشمار میرود. اگر میخواهید بدانید این فرآیند چگونه کار میکند، چه تکنولوژیهایی در آن بهکار میرود و چگونه میتوان کیفیت گرانول را ارتقا داد، این مقاله را تا انتها دنبال کنید.
تولید گرانول پلاستیک چیست؟
تولید گرانول پلاستیک فرآیندی فنی و مرحلهبهمرحله است که در آن مواد اولیه پلیمری، شامل پلیمرهای نو یا بازیافتی، طی مراحل ذوب، اکستروژن، برش و خنکسازی، به دانههای کوچکی به نام گرانول تبدیل میشوند. این گرانولها بهعنوان ماده اولیه در صنایع مختلف مانند تزریق پلاستیک، قالبگیری، فیلمسازی و حتی چاپ سهبعدی به کار میروند. گرانولها از نظر ابعاد، ترکیب شیمیایی، میزان رطوبت و شاخص جریان مذاب کنترلشده هستند، تا در فرآیندهای بعدی عملکرد دقیقتری ارائه دهند.
خط تولید گرانول بهعنوان پایهگذار فرآیندهای تولیدی در صنعت پلیمر، به نحوی طراحی میشود که قابلیت پردازش طیف وسیعی از مواد را داشته باشد. بسته به نوع ماده اولیه، میتوان از سیستمهای تکپیچه یا دوپیچه استفاده کرد. این فرایند، به دلیل نقش مهمی که در تبدیل ضایعات به محصول قابلاستفاده دارد، امروزه یکی از پایههای توسعه پایدار در صنایع پلاستیکسازی و بازیافت به شمار میآید.
مواد اولیه در تولید گرانول پلاستیک؛ چه انتخابهایی داریم و چرا اهمیت دارد؟
در فرآیند تولید گرانول پلاستیک، انتخاب مواد اولیه نقش حیاتی در تعیین کیفیت محصول نهایی دارد. این مواد میتوانند از منابع نو (مثل پلیاتیلن خالص یا پلیپروپیلن صنعتی) یا از ضایعات پلاستیکی بازیافتی تهیه شوند. نوع پلیمر، شاخص جریان مذاب، درصد ناخالصی و میزان رطوبت از جمله عواملی هستند که باید پیش از ورود به خط تولید بررسی شوند.
در مجتمع صنعتی کاجاران، به عنوان یکی از مراکز پیشرو در حوزه تولید گرانول، فرایند انتخاب و آمادهسازی مواد اولیه تحت استانداردهای دقیق کنترل میشود. استفاده از دستگاههای پیشرفته آنالیز و خشککنهای خاص، کمک میکند تا هرگونه ناخالصی یا رطوبت پیش از فرآیند اکستروژن حذف شود. این موضوع، علاوه بر ارتقاء کیفیت گرانول، موجب کاهش استهلاک دستگاهها و بهبود فرآیندهای بعدی میشود. مواد اولیه باکیفیت نه تنها باعث تولید گرانول یکنواخت و مقاوم میشوند، بلکه بازدهی خطوط تولیدی بعدی مانند قالبگیری تزریقی یا ساخت فیلمهای بستهبندی را نیز افزایش میدهند.
آمادهسازی مواد اولیه؛ پیشنیاز موفقیت در خط تولید گرانول
یکی از مراحل کلیدی در تولید گرانول پلاستیک، آمادهسازی دقیق مواد اولیه است. این مرحله پیش از ورود مواد به اکسترودر انجام میشود و شامل خشککردن، خردکردن، جداسازی ناخالصیها و در برخی موارد افزودن پایدارکنندههاست. برای مثال در خط تولید لولههای پلیاتیلن، کیفیت اولیه مواد تأثیر مستقیمی بر استحکام، یکنواختی و عملکرد نهایی لوله دارد. در این نوع کاربرد، کوچکترین ناخالصی یا رطوبت، میتواند موجب ترک، تغییر رنگ یا کاهش مقاومت لوله شود.
مواد پلیمری معمولاً در خشککنهایی با کنترل دمای دقیق قرار میگیرند تا رطوبت سطحی و داخلی آنها حذف شود. استفاده از غربالهای مغناطیسی نیز به حذف ذرات فلزی کمک میکند. همچنین، افزودن درصد معینی از افزودنیها نظیر پایدارکننده UV یا رنگدانهها در این مرحله، میتواند کیفیت نهایی گرانول را بهینه کند. آمادهسازی درست مواد، راهی مطمئن برای کاهش اتلاف، افزایش طول عمر تجهیزات و تضمین کیفیت در مراحل بعدی تولید است.
اکسترودینگ در تولید گرانول؛ قلب فرآیند تولید و تکنولوژیهای جدید
در فرآیند تولید گرانول پلاستیک، اکسترودر بهعنوان هسته مرکزی سیستم عمل میکند. مواد اولیه آمادهشده، وارد سیلندر اکسترودر میشوند، جایی که در اثر گرما و فشار بالا ذوب شده و به حالت مذاب یکنواخت درمیآیند. سپس این ماده مذاب از یک دای خاص عبور داده شده و آماده برش به گرانول میشود.
در خط تولید لوله پلیپروپیلن، استفاده از اکسترودرهای دوپیچه با کنترل دقیق دما، توزیع یکنواخت افزودنیها و ترکیب بهتر مواد، نقش مهمی در تولید گرانول با کیفیت بالا دارد. اکسترودرهای مدرن امروزی به سیستمهای هوشمند کنترل فشار، سرعت و گشتاور مجهز هستند و میتوانند متناسب با نوع پلیمر و کاربرد نهایی، فرآیند ذوب را تنظیم کنند.
با توجه به تنوع پلیمرهای مصرفی و ویژگیهای فیزیکی موردنیاز در محصولات نهایی، انتخاب نوع اکسترودر و پارامترهای تنظیمی آن، یکی از حیاتیترین تصمیمات در طراحی خط تولید محسوب میشود. یک فرآیند اکستروژن دقیق، ضامن کیفیت، یکنواختی و دوام گرانول است.
روشهای تبدیل پلیمر ذوبشده به گرانول؛ کاترینگ، استرندینگ و اسپری واتر
پس از خروج پلیمر مذاب از اکسترودر، فرآیند تبدیل آن به گرانولهای یکنواخت آغاز میشود. سه روش اصلی برای این مرحله وجود دارد: کاترینگ (برش مستقیم)، استرندینگ (تبدیل به رشته و سپس خردکردن)، و اسپری واتر یا Water Ring (برش در محیط آب).
در روش کاترینگ، پلیمر مذاب مستقیماً توسط تیغههای چرخان بریده شده و گرانول تولید میشود. این روش بیشتر برای پلیمرهای نرم و با ویسکوزیته پایین بهکار میرود. در روش استرندینگ، پلیمر ابتدا به صورت رشتهای از دای خارج شده، در آب خنک میشود و سپس توسط آسیابهای خاص خرد میگردد. این روش بهویژه برای گرانولهایی که باید خواص مکانیکی خاصی داشته باشند مناسب است.
روش اسپری واتر، ترکیبی از خنکسازی و برش همزمان است و در آن، گرانولها بلافاصله پس از خروج از دای، در محیط آبی خنک شده و برش میخورند. انتخاب روش برش، وابسته به نوع پلیمر، ظرفیت تولید، خواص فیزیکی موردنیاز و طراحی خط است. این مرحله تأثیر مستقیم بر یکنواختی ابعاد گرانول و کیفیت بستهبندی نهایی دارد.
سیستم خنککاری گرانول؛ تکنیکهای نوین برای افزایش کیفیت محصول نهایی
در مرحله خنکسازی، گرانولها پس از برش نیاز به پایین آوردن سریع دما دارند تا شکل، استحکام و خواص فیزیکی خود را حفظ کنند. روشهای مختلفی برای خنککاری وجود دارد که بسته به نوع پلیمر و طراحی خط، یکی از آنها انتخاب میشود. دو روش رایج، خنککاری با آب و خنککاری با هوا هستند.
در خنککاری با آب، گرانولها بلافاصله پس از برش وارد حوضچه آب یا سیستم اسپری میشوند تا دمای آنها سریعاً کاهش یابد. این روش برای پلیمرهای حساس به دمای بالا مانند پلیاتیلن و پلیپروپیلن رایج است. در مقابل، سیستمهای خنککاری با هوا برای تولید گرانولهایی بهکار میروند که نسبت به جذب رطوبت حساساند.
فناوریهای نوین امروزی از سیستمهای ترکیبی استفاده میکنند؛ مثلاً سیستمهای Air-Water Cooling که همزمان از جریان هوا و آب بهره میبرند تا خنککاری سریعتر و یکنواختتری انجام شود. انتخاب روش صحیح، علاوه بر بهبود کیفیت، از چسبیدن گرانولها به یکدیگر و ایجاد نقص در شکلگیری آنها جلوگیری میکند.
خشککردن گرانول پلاستیک؛ چگونه از مشکلات فیزیکی جلوگیری کنیم؟
پس از خنککاری، گرانولها معمولاً مرطوب هستند و رطوبت باقیمانده میتواند در فرآیندهای بعدی مانند قالبگیری یا اکستروژن مجدد، مشکلاتی ایجاد کند. بههمین دلیل، خشککردن یکی از مراحل کلیدی در تولید گرانول پلاستیک بهشمار میرود.
اگر گرانولها بهخوبی خشک نشوند، بخار حاصل از رطوبت در حین ذوب باعث ایجاد حفرهها، ضعف در ساختار محصول و کاهش مقاومت مکانیکی آن میشود. بهطور معمول، خشککنهای جریان هوای گرم (Hot Air Dryers) یا خشککنهای جذبکننده رطوبت (Desiccant Dryers) برای این منظور استفاده میشوند.
مدتزمان و دمای خشککردن باید متناسب با نوع پلیمر تنظیم شود. برای مثال پلیکربنات یا PET به خشککردن عمیقتری نیاز دارند تا رطوبت درونی آنها نیز از بین برود. استفاده از سنسورهای رطوبت برای نظارت بر این مرحله، یکی از راهکارهای علمی برای افزایش دقت و کاهش خطا در تولید گرانول است. خشککردن مناسب، تضمینی برای عملکرد بهینه گرانول در مراحل صنعتی بعدی خواهد بود.
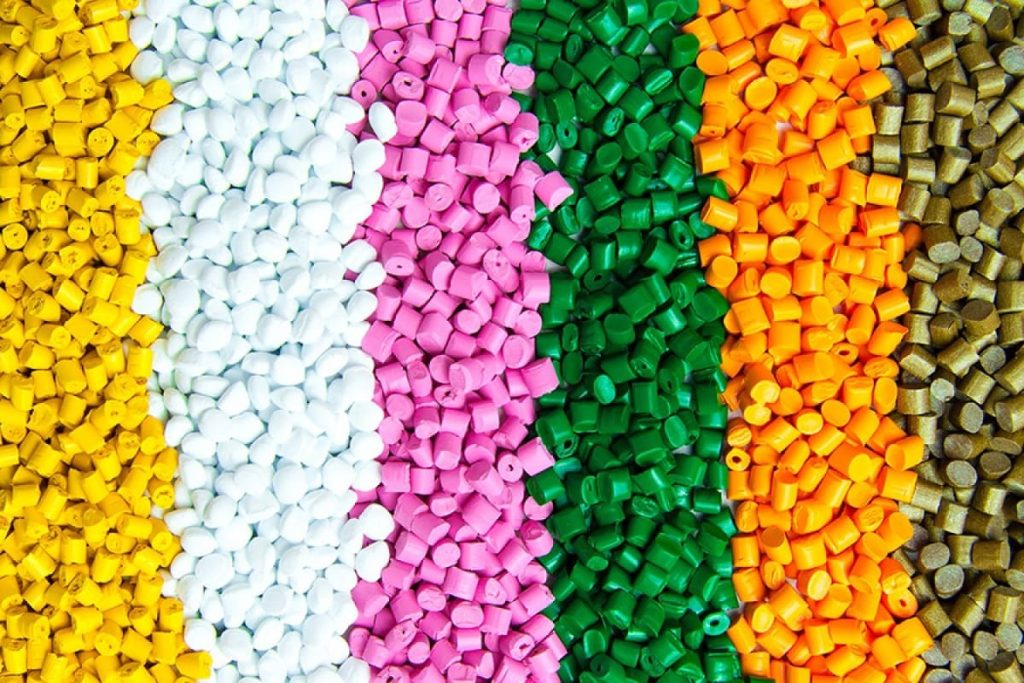
دستهبندی، بستهبندی و ذخیرهسازی گرانول؛ اصول علمی برای ماندگاری بیشتر
پس از تولید و خشککردن، گرانولها باید با دقت دستهبندی و بستهبندی شوند تا خواص فیزیکی و شیمیایی آنها حفظ شود. دستهبندی بر اساس اندازه ذرات، نوع پلیمر و ویژگیهای فنی انجام میشود. در این مرحله از الکها، سیستمهای نقاله هوشمند و سنسورهای نوری برای بررسی یکنواختی ابعاد استفاده میشود.
بستهبندی گرانولها معمولاً در کیسههای صنعتی چندلایه با قابلیت ضد رطوبت یا در مخازن صنعتی انجام میگیرد. در صورت تماس با رطوبت یا آلودگی، کیفیت گرانول بهشدت افت میکند و در بسیاری از موارد غیرقابل استفاده میشود. بههمین دلیل، انبار نگهداری گرانولها باید دارای سیستم تهویه و کنترل دما باشد.
در شرایط ایدهآل، دمای محیط ذخیرهسازی باید پایین و ثابت باشد و از نور مستقیم خورشید جلوگیری شود. همچنین، نباید گرانولها در مجاورت مواد شیمیایی یا خورنده قرار گیرند. رعایت این نکات، علاوهبر حفظ کیفیت گرانول، باعث افزایش عمر مفید آن در زنجیره تأمین صنعتی میشود.
کنترل کیفیت در تولید گرانول؛ معیارهای تست و تکنیکهای بهبود مستمر
در فرآیند تولید گرانول پلاستیک، کنترل کیفیت بهصورت مداوم انجام میشود تا اطمینان حاصل شود که محصول نهایی مطابق با استانداردهای صنعتی است. اولین و مهمترین شاخص، Melt Flow Index (MFI) یا شاخص جریان مذاب است که میزان جریانپذیری گرانول را مشخص میکند. این شاخص برای تنظیم دمای ذوب در دستگاههای تزریق یا اکستروژن بسیار حیاتی است.
دیگر آزمونها شامل بررسی چگالی، مقاومت حرارتی، اندازه ذرات، درصد رطوبت و یکنواختی رنگ هستند. در خطوط تولید پیشرفته، تجهیزات آنلاین کنترل کیفیت بهصورت خودکار هر دسته از گرانول را بررسی کرده و در صورت انحراف از محدوده استاندارد، هشدار ارسال میکنند یا مواد معیوب را از چرخه خارج میسازند.
برای بهبود مستمر کیفیت، از روشهایی مانند کنترل آماری فرآیند (SPC)، بهینهسازی فرمولاسیون و بررسی عملکرد دورهای ماشینآلات استفاده میشود. اجرای برنامههای نگهداری پیشگیرانه نیز از خرابیهای ناگهانی دستگاهها و افت کیفیت محصول جلوگیری میکند. در نتیجه، کنترل کیفیت دقیق نهتنها ضامن سلامت گرانول بلکه عامل اصلی رضایت مشتریان نهایی است.
بازیافت گرانولهای معیوب؛ چگونه دورریزها را به چرخه بازگردانیم؟
در هر خط تولید گرانول، بخشی از محصول ممکن است به دلایل فنی یا کیفی از استاندارد مورد نظر خارج شود. گرانولهایی که اندازه غیر یکنواخت، رطوبت بالا، ناخالصی یا خواص مکانیکی ضعیف دارند، بهعنوان محصول معیوب شناخته میشوند. اما این بهمعنای هدررفت نیست؛ بلکه با رویکردهای علمی، میتوان این مواد را دوباره وارد چرخه تولید کرد.
برای بازیافت این گرانولها، ابتدا آنها از محصول نهایی جدا شده و مجدداً خرد، خشک و ترکیب میشوند. در برخی موارد، نیاز است این مواد با پلیمر نو یا افزودنیهای خاص ترکیب شوند تا ویژگیهای لازم بازیابی گردد. بازیافت داخلی در خطوط تولید نهتنها به کاهش ضایعات کمک میکند، بلکه از نظر اقتصادی نیز بسیار مقرونبهصرفه است. البته برای اطمینان از کیفیت، باید محدودیتهایی در میزان استفاده از گرانول بازیافتی اعمال شود. رعایت این اصول، امکان تولید پایدار، کاهش هزینهها و حفظ منابع را برای صنایع فراهم میسازد.
کاربرد گرانول پلاستیک در صنایع مختلف؛ از خودروسازی تا تجهیزات پزشکی
گرانول پلاستیک بهدلیل تنوع بالا در ساختار و خواص، کاربرد گستردهای در صنایع مختلف دارد. در صنعت خودروسازی، از گرانولهای پلیپروپیلن و ABS برای ساخت داشبورد، سپر و قطعات داخلی استفاده میشود. در صنعت بستهبندی، پلیاتیلن با دانسیتههای مختلف برای تولید فیلم، کیسه و بطری کاربرد دارد. صنایع پزشکی نیز از گرانولهای خاص با خلوص بالا و زیستسازگار برای تولید تجهیزات استریل و یکبار مصرف بهره میبرند. گرانولهای PVC نیز در صنعت ساختمان برای تولید پروفیل، لوله، در و پنجره استفاده میشوند.
با افزودن کامپاندهای مختلف به گرانولها، میتوان ویژگیهایی چون مقاومت در برابر شعله، ضد UV، آنتیباکتریال و رنگبندی خاص را به آنها افزود. همین انعطاف بالا باعث شده تا گرانولها در خطوط تولید متنوع با تکنولوژیهای تزریق، اکستروژن و بادیمولدینگ بهکار گرفته شوند. در نتیجه، گرانولها نهتنها ماده اولیه، بلکه قلب تپنده صنعت پلاستیک بهشمار میآیند.
جمعبندی: چرا تولید گرانول پلاستیک یک حلقه حیاتی در صنعت است؟
تولید گرانول پلاستیک فراتر از یک فرآیند صنعتی ساده، نقش یک حلقه حیاتی در زنجیره تولید محصولات پلیمری را ایفا میکند. این فرآیند به صنایع اجازه میدهد تا از منابع بهصورت پایدارتر بهرهبرداری کنند، ضایعات را به محصولات باارزش تبدیل نمایند و در عین حال کیفیت و سازگاری فنی مواد اولیه را برای کاربردهای متنوع تضمین کنند. با پیشرفت فناوری، اکنون امکان کنترل دقیق خواص فیزیکی و شیمیایی گرانولها فراهم شده است. این قابلیت، صنایع مختلف از جمله خودروسازی، بستهبندی، پزشکی و کشاورزی را قادر ساخته تا محصولات خود را با استانداردهای جهانی تولید کنند.
از انتخاب ماده اولیه گرفته تا خشککردن، اکستروژن، برش و بستهبندی، هر مرحله در تولید گرانول پلاستیک نیازمند دانش تخصصی، ماشینآلات دقیق و نظارت کیفی مستمر است. توجه به جزئیات این فرآیند، کلید کاهش هزینهها، ارتقای کیفیت و افزایش رقابتپذیری در بازار است. اگر به دنبال راهاندازی یک خط تولید هستید یا میخواهید کیفیت گرانول خود را بهینه کنید، دانش عمیق از این چرخه برای شما حیاتی خواهد بود.
سوالات متداول
۱. آیا میتوان از ضایعات پلاستیکی برای تولید گرانول استفاده کرد؟
بله، بسیاری از خطوط تولید گرانول از ضایعات بازیافتی بهره میبرند، به شرطی که فرآیند آمادهسازی و جداسازی ناخالصیها بهدرستی انجام شود.
۲. گرانولهای تولیدی در چه صنایعی مصرف میشوند؟
در صنایع بستهبندی، خودروسازی، پزشکی، کشاورزی، ساختمانی، لوازم خانگی و اسباببازی کاربرد دارند.
۳. تفاوت اکسترودر تکپیچه و دوپیچه در چیست؟
اکسترودر تکپیچه سادهتر و ارزانتر است، ولی اکسترودر دوپیچه توانایی ترکیب بهتر مواد، افزایش یکنواختی و کنترل دقیقتر را دارد.
۴. چگونه کیفیت گرانول را کنترل میکنند؟
با استفاده از شاخصهایی مانند MFI، چگالی، میزان رطوبت، یکنواختی رنگ و اندازه ذرات، و با بهرهگیری از تجهیزات آزمایشگاهی یا کنترل آنلاین.
۵. چه عواملی باعث کاهش کیفیت گرانول میشود؟
ناخالصی در ماده اولیه، خشکنکردن مناسب، نوسان دمای اکسترودر، رطوبت بالا و بستهبندی نامناسب.